Smelters Belting
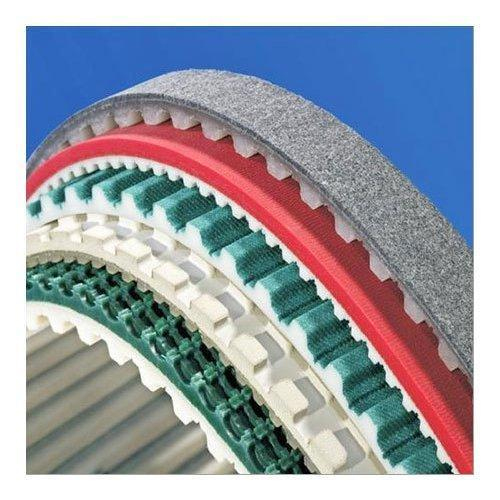
Belts used in Smelters
Smelters Belting is more into melting the metal out of its ore. For that purpose, belting systems are used in these industries to carry raw iron ore into the furnace and carrying it outside the furnace. To produce the metal in these industries, these compounds have to undergo a chemical reaction with the help of belting system.
Task Performed
- Roasted iron ore is stockpiled along with limestone for flux and coke for fuel
- After measurement of the material in the charging house and the material is tipped into the furnace
- The contents grew incredibly hot as they settled in the furnace.
- At 1,500 degree Celsius it is turned into a molten mass of iron and slag
- The floating slag on top was drained into wagons using conveyor belts
- After one last draining of slag the iron was tapped from a lower hole
- The molten content branched into sows and pigs until it ceased to flow
- When the content is solidified they were dug out and the sand was prepared for the next tapping
- A few hours later the furnace was ready to be tapped again
Technology Support
Conveyor belts carry out a wide range of conveyor tasks in smelting industries. These are used for conveying high temperature raw materials or for the transport of goods containing grease and oil, for steep-incline conveying and with special reinforcing materials for particular applications.
Benefits of Belting Systems in Smelters
- Handling and transportation of hot Molten mass of Iron
- Provides horizontal, steep as well as vertical transport
- Provides Safe and Secure transportation of hot content from furnace